What is this about?
In March 2023, a hazardous chemical spill occurred in the plant room of a Belgravia Leisure venue.
During the morning pre-open plant room check at 5:30am, the Duty Manager noticed chemical gas/vapor escaping from the hydrochloric acid room.
The venue was evacuated, and emergency services were called.
Subsequent investigation found a hydrochloric acid pump overflow pipe was incorrectly directed to an unfit receiving vessel which overflowed during the night into the hydrochloric acid pump room instead of being directed back into the hydrochloric acid bulk storage container with separate bunding.
The venue was closed for two days for plant maintenance to occur, which included the installation of an adequate overflow protection system.
Thankfully no one was injured during the incident.
What you need to know:
- Most of the plant chemicals used in our aquatic venues are hazardous chemicals, potentially posing physical, health or environmental hazards.
- All Belgravia team members and other persons at the workplace have duties under the WHS Act to identify and manage the risks associated with plant and hazardous chemicals.
- This usually starts with a formal risk assessment process to assess the risks involved and address the control measures to put in place to mitigate those risks.
How does this happen?
- Only have chemicals that your venue use, at your venue.
- Ensure you have a Safety Data Sheet (SDS) for each chemical.
- Ensure all hazardous chemicals have a Chemical Risk Assessment and Safe Operating Procedure in place.
- When doing a plant room risk assessment, consider the environmental aspects such as bunding for chemical spills, spill kits and atmospheric monitoring.
- Ensure you have a Chemical Register for the venue in place.
How to prevent similar incidents:
- Designing and implementing planned maintenance programs for chemical handling systems.
- Installing overflow protection on equipment and receiving vessels.
- Maintaining a safe atmosphere in the storage and handling areas.
- Ensuring Risk Assessments are updated, controls are maintained and periodically reviewed.
- Providing a spill containment system/s, where incompatible chemicals will not be brought into contact with one another.
- Using contractors to undertake plant maintenance and manual handling of chemicals where needed.
The ask:
Please take some time over the coming week to review your plant room and chemical management system, preventative maintenance schedules, spill kits and environmental management plan.
If you are unsure about potential environmental of safety-related risks in your plant room, speak to your Area or Regional Manager – someone from within Belgravia, or an external company can provide support with diagnosing improvements.
Take the measures to ‘Think Safe Act Safe Be Safe’ about our chemical and environmental management.
More information on can be found on the Safe Work Australia website or following the Code of Practice link below.
Code of Practice: Managing risks of hazardous chemicals in the workplace.
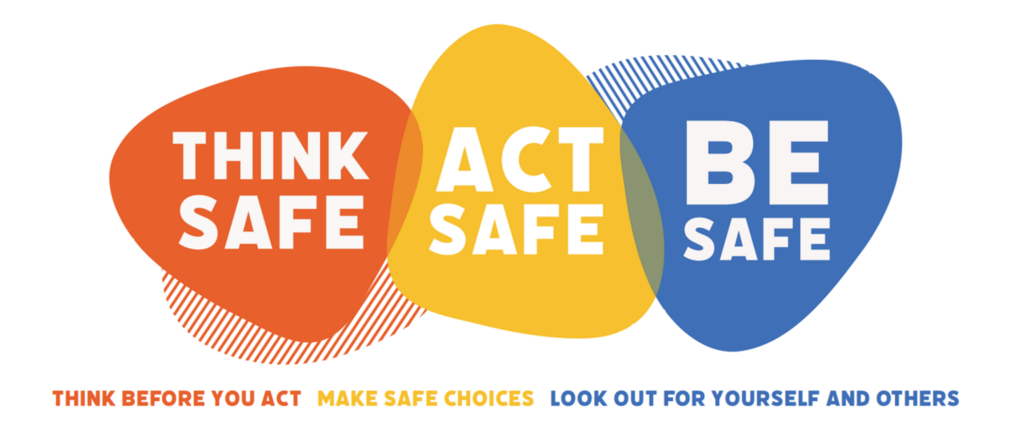
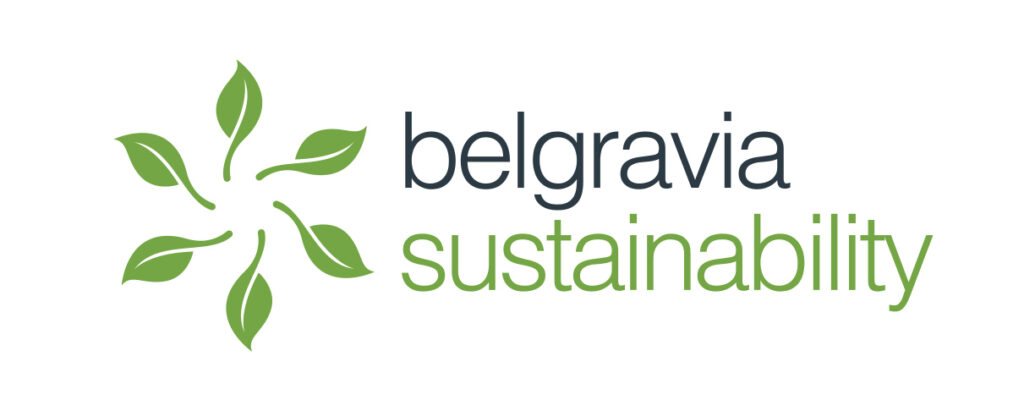